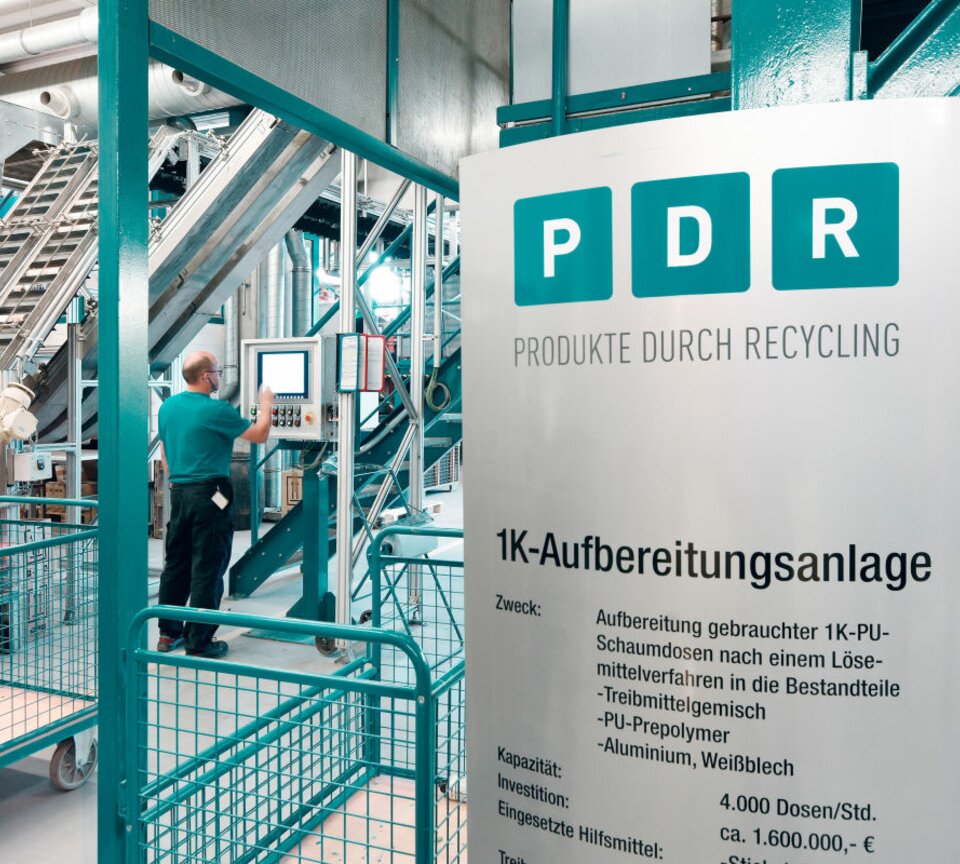
Turning old into new: recycling polyurethane foam cans
For technical reasons, it is not possible to empty a polyurethane foam can completely. Residual amounts of liquid prepolymer and foaming agent remain in the can – valuable materials that can be returned to the production process. Due to these ingredients, which are classified as harmful to health, used polyurethane foam cans are considered hazardous waste. Therefore, polyurethane foam cans do not belong in residual waste, plastics recycling, construction or tinplate waste. PDR Recycling GmbH + Co KG offers an environmentally friendly alternative to expensive hazardous waste disposal. It is a joint venture of the leading European manufacturers of polyurethane foam cans, based in Germany. Via a convenient collection and return system, PDR is able to collect used polyurethane foam cans on the German market, transport them to their site in Thurnau and recycle them.
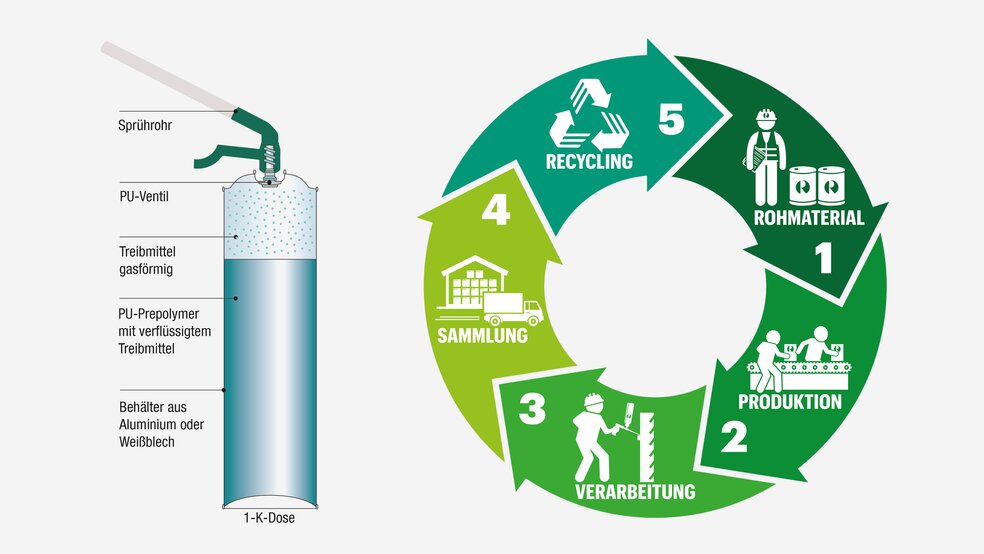
The Germany-wide collection of used polyurethane foam cans works through cooperation with logistics partners. Deutsche Post AG also collects individual return boxes from users. In this way, used polyurethane foam cans reach the recycling plant in Thurnau from all parts of Germany. Consumers do not incur any additional costs: the return service is included in the sales price of the cans. Professionals (e.g. tradesmen or construction companies) collect the used polyurethane foam cans in the original packaging (return box). Once the box is full, they simply request collection within Germany by toll-free fax (+49 (0)800 7836737) or telephone (+49 (0)800 7836736). PDR will then organise the removal of the cans from the company or even the construction site. Standing orders can also be arranged for regular collections. The logistics partner will then get in touch a few days in advance to confirm the exact collection date for the boxes. DIYers can hand in individual cans at their local collection point for hazardous waste or at a retailer, where they are also collected by the PDR logistics partners.
Disposal
Currently, the recycling of used polyurethane foam cans via PDR is only possible in Germany. In Austria, disposal takes place via the ARA system.
Disposal in Germany:
PDR Recycling GmbH + Co KG, Am alten Sägewerk 3, 95349 Thurnau, Germany
Tel: +49 (0)800 7836736, Web: www.pdr.de, Email: info@pdr.de
Disposal in Austria:
www.ara.at/d/partner/entsorgungspartnerverzeichnis.html
Used polyurethane foam cans are returned in the original sales carton or in the UN-coded return carton. In the so-called washing screw, the metal parts of the previously mechanically crushed 1-component polyurethane foam cans are cleaned. The cleaned and dried aluminium and tinplate parts travel via a conveyor belt for re-sorting. The metal recovered in this way is remelted in a metal smelter. The product TRIGAS® is filled into pressurised drums and delivered to industry for use in new aerosol products.
Closed production cycle
At its recycling plant in Thurnau, PDR operates a special facility for recycling used polyurethane foam cans. This plant, which is unique worldwide, can process up to 4,000 cans per hour. With state-of-the-art technology, PDR achieves a recycling rate of over 95%, of which 80% is material. This means that there is a closed product cycle for polyurethane foam cans. The sorted 1-component polyurethane foam cans are transported via a conveyor belt to the processing plant where they are first mechanically crushed in the absence of air. The liquid contents and the metal parts of the can containers (aluminium or tinplate) fall into a solvent bath. The metal parts are conveyed out of the solvent bath by a washing screw and pre-washed with the help of washing nozzles.
In a second washing stage, they are cleaned again with clean solvent. The clean metal parts with solvent deposits are then fed into a drying screw. The solvent residues are removed by supplying evaporation energy. The cleaned and dry metal parts then pass through the exit sluice and are sorted into aluminium and tinplate containers. The metal obtained in this way is remelted in a metal smelter.
The polyurethane-solvent mixture that accumulates below the shredding system is fed via a filter station to the polyurethane treatment unit, where the solvent content is removed. This is used again to wash the metal parts. The recovered secondary raw material is filled into transport containers and can be used again by the industry. The propellants released from the polyurethane foam cans are extracted above the shredding system and transported to the propellant recovery unit. Filled into pressurised gas containers, they are then available to the aerosol industry for use in special applications. The cardboard packaging is also either reused or sent to a recycler.
2-component polyurethane foam cans are processed in a separate plant that functions in a similar way. The cans are mechanically shredded. Metal is separated from polyurethane foam residues, cleaned and re-sorted. Foaming agents are extracted and processed. No liquid parts of polyurethane remain in 2-component polyurethane foam cans, as it already cures completely in the cans during the application procedure. These hardened polyurethane foam residues are also separated and collected. They are then sent for energy recovery.